Regardless of whether you’re an upstream, midstream, or downstream producer in the oil & gas ind...
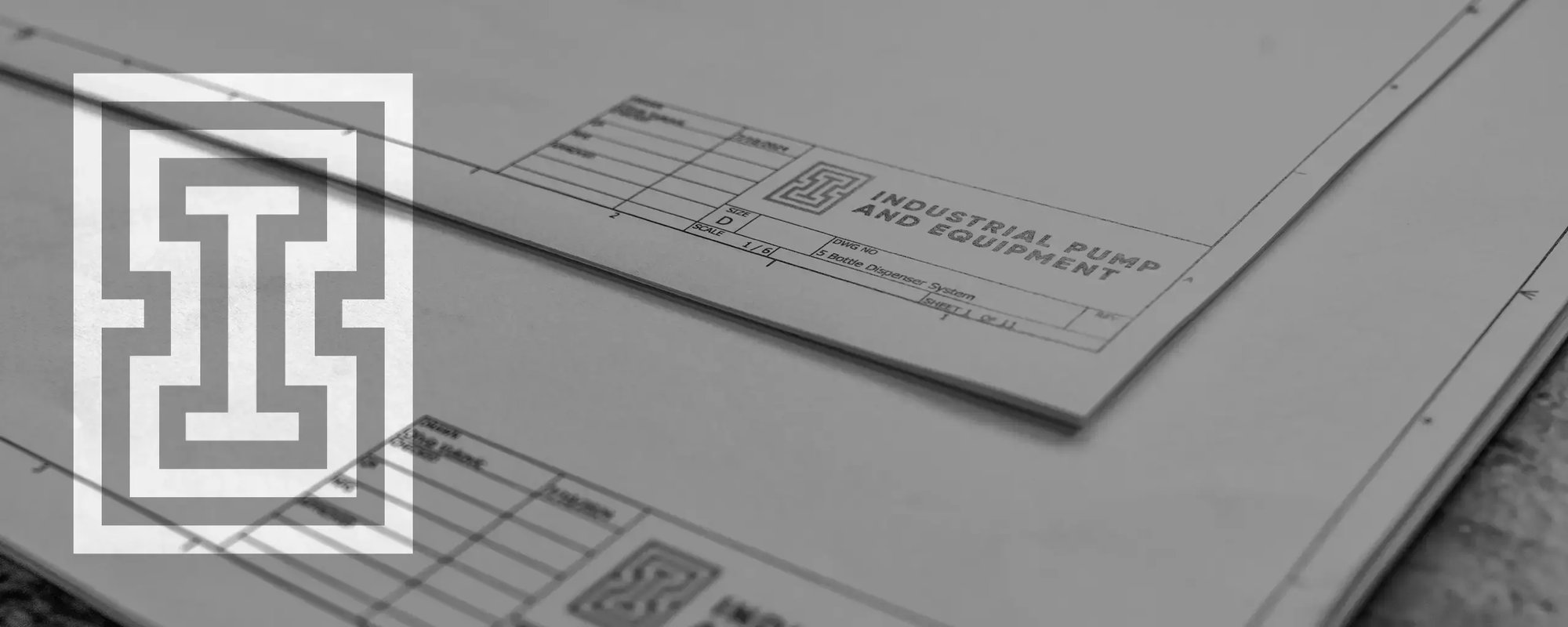
Latest news
Time for a Check Up: Why Regular Maintenance Checks Are Important for Pump and Compressor Efficiency
The demands of modern manufacturing means plant operators need equipment that maximizes uptime, espe...
For today’s plant engineers, selecting the ideal industrial compressor for your application or chall...
A quality foundation is critical to the stability of any structure, whether it’s a house, office bui...
Today’s oil & gas industry has a very distinct set of challenges plant operators and engineers m...
The ability to optimize fluid management in several major industrial landscapes is based on pump sys...
When it comes to API pump applications, the most common challenge is identifying the most reliable a...
A precise, efficient water metering system is key for any industrial application that requires water...
What are the main differences between centrifugal and reciprocating industrial pumps? From pump cons...
You may not immediately associate concrete batching with creating a recipe for a cake or a pie, but ...